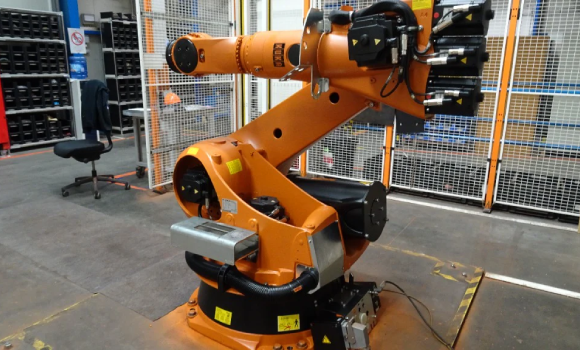
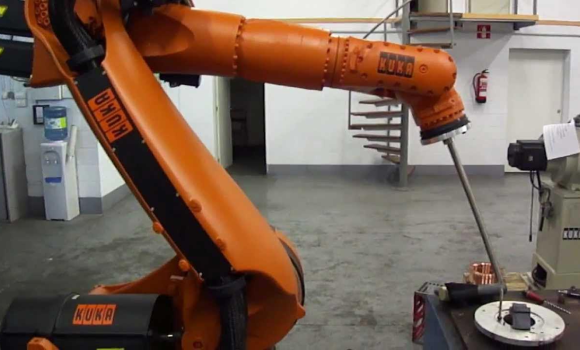
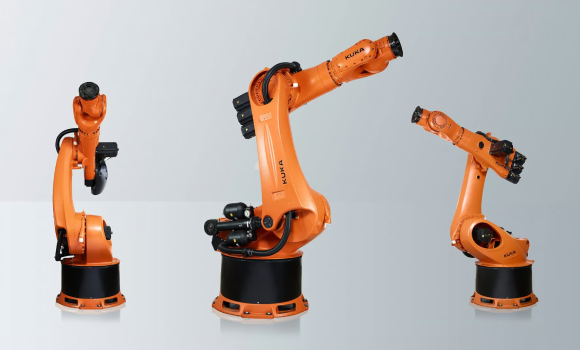
Specifications:
The robot arm utilizes epicyclic (planetary) gearboxes for the significant hub and is both basic and solid. It ought to be noticed that the arm is additionally exceptionally tough and is less helpless against harm than a considerable lot of its rivals. The robot is altogether fueled by air conditioning servo engines, the “rams” in favor of the arms are not water powered or pneumatic, they are essentially encased mechanical springs. The springs and load on the back of the robot make it exceptionally all around adjusted significance the powers required to move the robot are surprisingly little. Future or MTBF (mean time between disappointment) is to a great extent subject to benefit rehearses (when a year is typical) however we anticipate that 6400’s should keep going for somewhere around 100,000 hours. Having said this we have seen genuine models with substantially more than this. These are the primary kinds of S4 controlled IRB 6400 model, costs can rely upon the accessibility of a specific model, for instance, the 3.0m reach is nearly uncommon: