Welding Automation
Welding automation in manufacturing refers to the use of robotic systems, mechanized tools, and automated processes to perform welding tasks, reducing the need for human intervention. It involves employing robotic arms, computer-controlled welding machines, and various sensors to carry out precise, consistent, and efficient welding operations. This technology is crucial in industries like automotive, aerospace, construction, and heavy machinery, where welding is a core part of production.
Key Parameters of Welding Automation
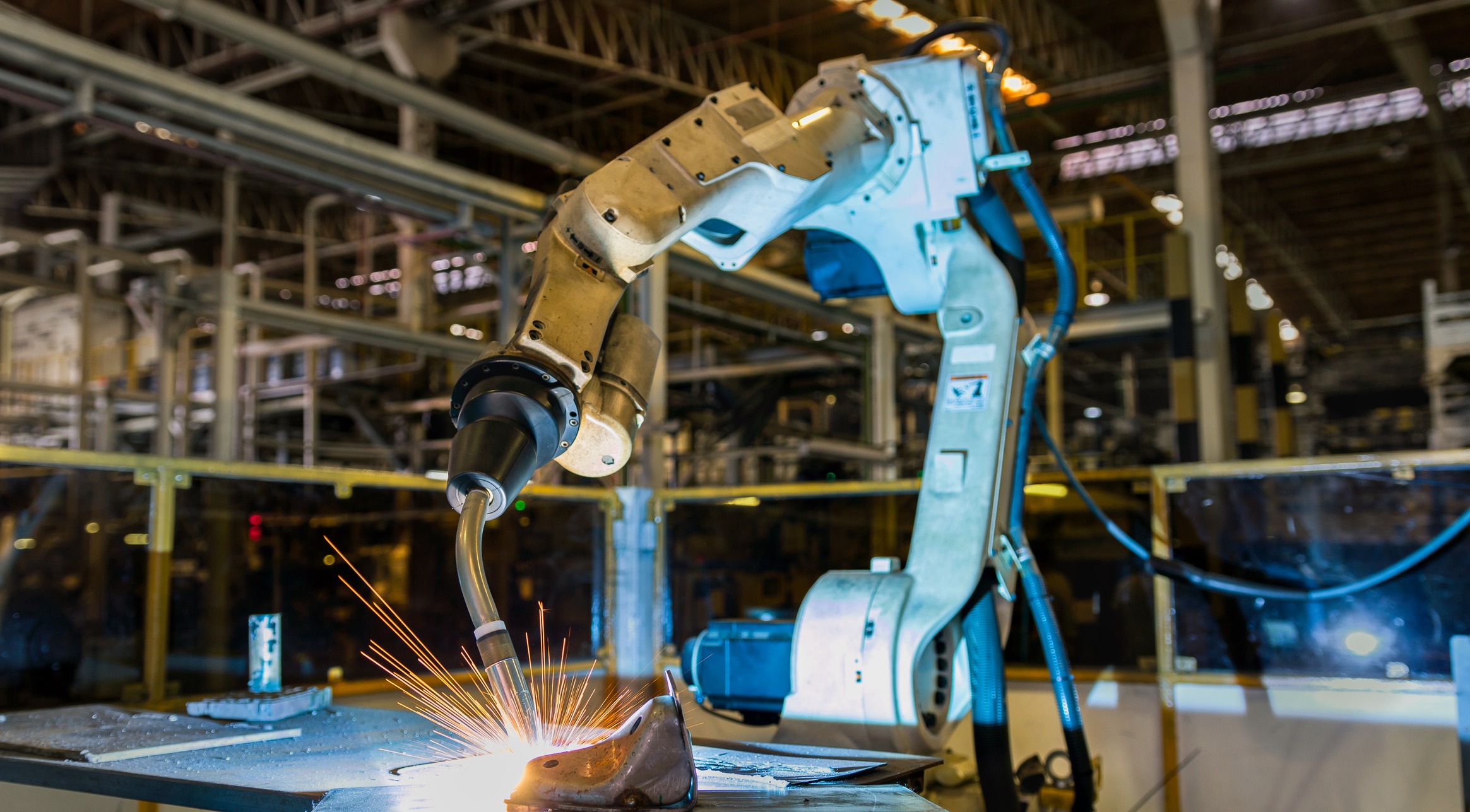
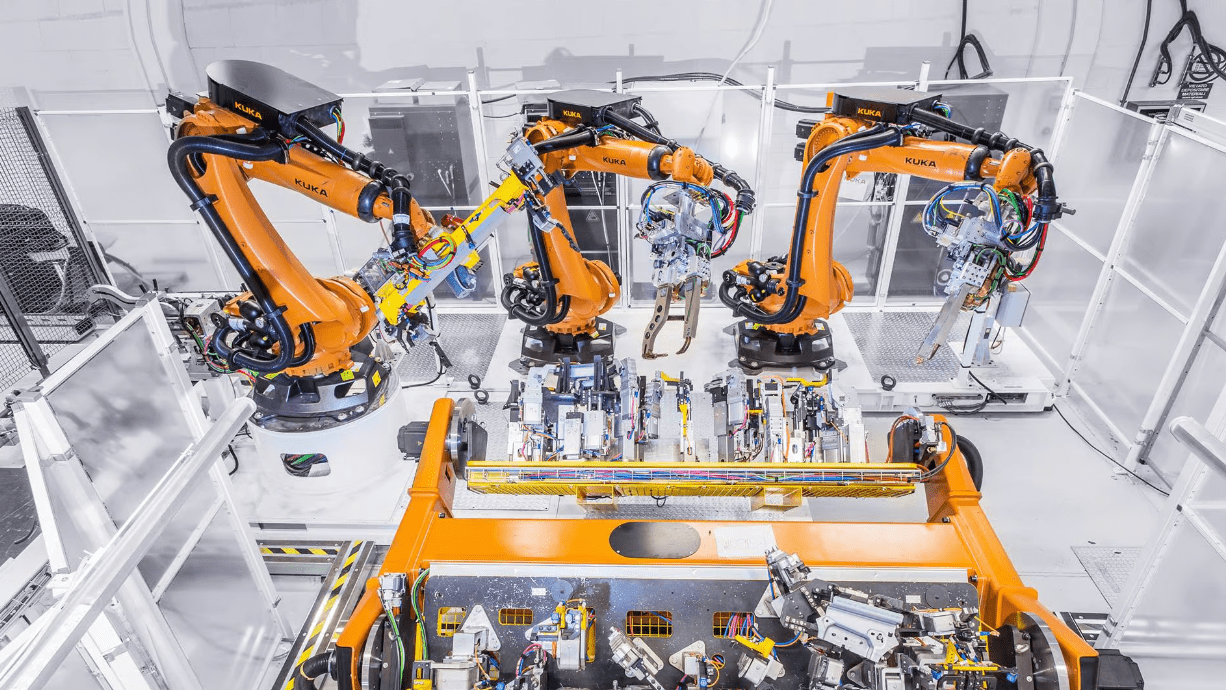
Payload Capacity
- Function: Capture images or video of the robot’s environment.
- Application: Used for object detection, identification, and navigation in robotics and automation systems.
Repeatability and Accuracy
- Function: Repeatability refers to a robot’s ability to perform the same task consistently, while accuracy indicates how closely the robot’s output matches the intended target.
Application: Both are critical in manufacturing processes, such as assembly and quality control, ensuring consistent and precise results in production.
Speed and Cycle Time
- Function: Speed refers to how fast a robot can perform a task, while cycle time is the total time taken to complete a specific operation or series of operations.
Application: Both are crucial in manufacturing and automation processes, as they impact overall productivity and efficiency, influencing throughput in assembly lines and other automated systems.
Number of Axes
- Function: The number of axes in a robotic system refers to the degrees of freedom it has, allowing for movement in different directions. Each axis typically corresponds to a joint or rotational point in the robot’s arm or body.
Application: The number of axes determines a robot’s flexibility and capability in performing complex tasks, such as welding, painting, or assembling components, making multi-axis robots suitable for intricate operations in manufacturing and automation.
Torch and Tool Mounting Options
- Function: Various methods to attach welding torches and tools to a robot, allowing for task-specific configurations.
Application: Essential for welding and fabrication, enabling robots to perform tasks like MIG, TIG, or plasma cutting efficiently and precisely.
Robot Welding Tool
- Function: Various methods to attach welding torches and tools to a robot, allowing for task-specific configurations.
- Application: Essential for welding and fabrication, enabling robots to perform tasks like MIG, TIG, or plasma cutting efficiently and precisely.
Integration with Welding Fixtures
- Function: Integration with welding fixtures to enhance the stability and accuracy of the welding process.
- Application: Crucial for ensuring proper alignment and positioning of workpieces, enabling robots to perform consistent and high-quality welds across various applications.
Applications of Welding Automation
Quality Control
- Tasks: Detect defects, measure dimensions, and verify the integrity of welds.
Industries: Manufacturing, automotive, aerospace.
Benefits: Ensures consistent product quality and reduces manual inspection costs.
Robotic Welding in Automotive Assembly
- Tasks: Perform spot welding and MIG welding for vehicle body parts.
Industries: Automotive.
Benefits: Increases production speed and accuracy while reducing labor costs.
Electronics Manufacturing
- Tasks: Soldering components onto circuit boards using automated soldering machines.
Industries: Electronics.
Benefits: Enhances precision and reduces the risk of damage to sensitive components.
Pipeline Welding
- Tasks: Automated welding of pipelines for oil and gas transport.
Industries: Oil and gas.
Benefits: Reduces labor costs and improves safety by minimizing manual handling in hazardous environments.
Pharmaceutical Equipment Fabrication
- Tasks: Weld stainless steel components for pharmaceutical manufacturing equipment.
Industries: Pharmaceuticals.
Benefits: Maintains hygiene standards and ensures structural integrity of equipment used in drug production.
Mahajan Automation, transforms welding processes with innovative solutions that boost precision and efficiency.
Benefits of Robotic Welding Automation
Increased Precision and Accuracy
- Explanation: Automated systems provide consistent control over welding parameters, resulting in high-quality welds.
- Application: Ensures precise weld placement and integrity across various applications.
Improved Productivity
- Explanation: Robots can operate continuously and at higher speeds than human welders.
Application: Increases overall production rates, allowing for greater output in manufacturing processes.
Enhanced Safety
- Explanation: Robots perform dangerous welding tasks, reducing the risk of injury to human workers.
Application: Creates a safer work environment by minimizing exposure to hazardous fumes and intense heat.
Cost Efficiency
- Explanation: Reduced labor costs and decreased material waste contribute to overall cost savings.
Application: Lower operational costs while maintaining high production standards.
Consistent Quality
- Explanation: Automated welding processes ensure uniformity and reduce variability in weld quality.
Application: Leads to fewer defects and rework, improving product reliability and customer satisfaction.
Flexibility and Adaptability
- Explanation: Robotic systems can be reprogrammed for different welding tasks and product types.
Application: Enables manufacturers to adapt quickly to changing production needs and designs.
What We Do
“A compelling way of generating innovative ideas”
Visual feedback is essential for image and vision-guided robots. Their power of sight is one of the elements that make them widely used across different disciplines.
Welding Seams in Welding Systems
Fully automated welding places great demands on quality and precision. Consequently, the correct position of the respective seam must be reliably detected before the welding process is started in the robot cell. Welding systems are equipped with innovative weCat3D 2D/3D profile sensors for the purpose of weld seam tracking.
- Image Processing
- Part Inspection
- De-Palletization and primary packaging
- Welding Seam Tracking
- Sorting
Solutions of Welding Automation
Robotic Welding Systems
Implement robotic arms equipped with welding torches for precision and efficiency in repetitive welding tasks.
Automated Welding Equipment
Use advanced welding machines with integrated sensors for real-time monitoring and adjustment of parameters.
Welding Positioners
Employ automated positioners to rotate and tilt workpieces, ensuring optimal angles for welding.
Vision Systems
Integrate machine vision technology to assist robots in detecting seams and ensuring accurate weld placement.
Data Analytics and Monitoring
Utilize software for tracking welding performance and quality, enabling predictive maintenance and process optimization.